A better process: A Better Product
Magnolia Bronze bushings and bearings, die cast in steel molds, remain absolutely free of any hidden sand particles which may damage the shaft. This unique casting process allows for a uniform, or “isotropic” crystal structure unlike that found in sand cast metals.
In addition to eliminating all pattern costs, the Magnolia method gives you a perfect bearing metal at a price often surprisingly lower than the original equipment manufacturer’s replacement part.
Send your own blueprint in detail for quoting and ordering purposes. We handle all inquiries promptly.
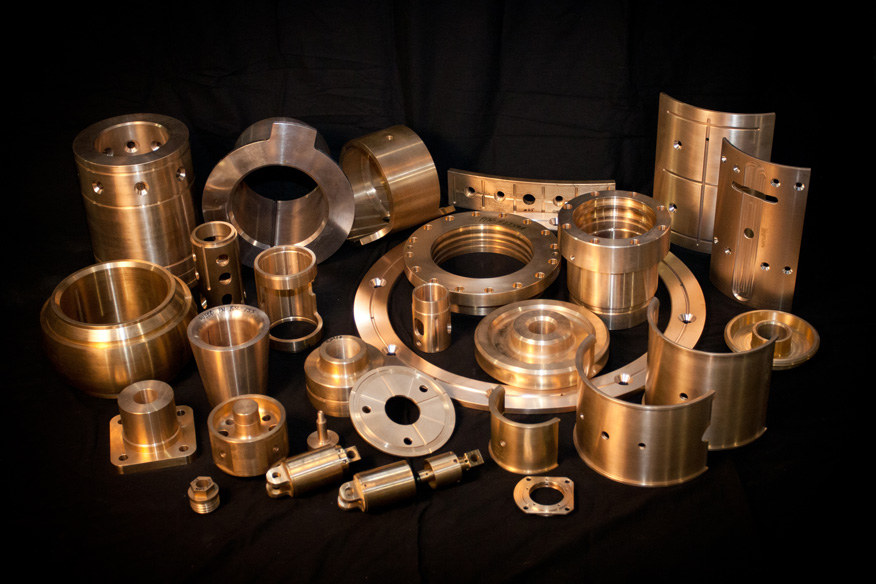
Ready-to-use parts machined to your blueprints
Magnolia bronze bearings are all either cast continuously or cast in steel. No sand is used in manufacturing. This entirely eliminates patterns and core boxes with savings passed on to you. Because all your machining can be done by Magnolia, you are saved additional machine time in your own plant, resulting in lower costs. All castings are machined. No bronze is shipped in an “as cast” state.
Magnolia steel-cast bronze wears much longer and is far tougher and stronger than the best sand cast product. Being absolutely free of any hidden sand particles insures a longer life for your shaft.
The Magnolia crystal control method of centrifugal casting allows for a uniform or “isotropic” crystal structure, unlike that found in sand cast metals, while raising physical characteristics far above the requirements for similar formula sand castings.
Some of our offerings include:
- Radii, keyways, oil grooves, windows and perfect halves.
- Large bronze blanks, steel-cast up to 34″ body O.D.; 26″ in length.
- Flange bushings through 34″ O.D. of flange.
- Drilling-grooving
- Sawcut halves and segments
- Split and sweat
- Windows – pockets
- Washers
- Rings
- Rectangles/square
Standard Commercial Machine Tolerance (Unless otherwise specified)
Inside Diameter:
Up to 3″ I.D. . . . . . . . . . . . . . ± .001″
3″ I.D. and up . . . . . . . . . . . . ± .0015″
Outside Diameter
Up to 3″ O.D. . . . . . . . . . . . . + .002″ to + .003″
3″ O.D. to 5″ . . . . . . . . . . . . . + .003″ to + .005″
5″ O.D. and up . . . . . . . . . . . + .003″ to + .006″
Concentricity (Total Indicator Reading)
3/4″ through 3″ O.D. . . . . . . . . . .003 maximum
Over 3″ through 8″ O.D. . . . . . . .004″ maximum
Over 8″ O.D. . . . . . . . . . . . . . . . .005 maximum
All lengths will be held to ± .005″
A better bronze: a better product CDA 936 Superior to CDA 932
Tests conducted in both a national laboratory and a major university confirm Magnolia CDA 936 consistenly outperforms CDA 932 (SAE 600) under the most difficult conditions in test after test.
CDA 936: Better because
- Higher lead content gives better lubricating properties and provides better co-efficient of friction. Bearings run cooler, last longer.
- One and a half times as resistant to pounding.
- Acid resisting to sulphite fluids due to lower zinc. CDA 936 can be used in areas where CDA 932 would corrode.
The best Bronze: Tested & Proven
Laboratory Tests Prove it!
Tests conducted by a national laboratory verify that Magnolia CDA 936 consistently out performs CDA 932 (SAE 660) under the most difficult conditions in test after test. The bearings were run with inadequate lubrication until temperatures exceeded 400ºF. Under these severe conditions, in some instances teh CDA 932 wore out three times faster than CDA 936. In no test did CDA 932 out perform CDA 936.
Newly completed tests by a major university also prove that Magnolia’s CDA 936 alloy has a significantly higher failure resistance than CDA 932. Despite extreme circumstances, operating without lubrication, CDA 936 ran an average of 78% longer than CDA 932, and with none of the incidents of severe shaft scoring found among the CDA 932 tests.
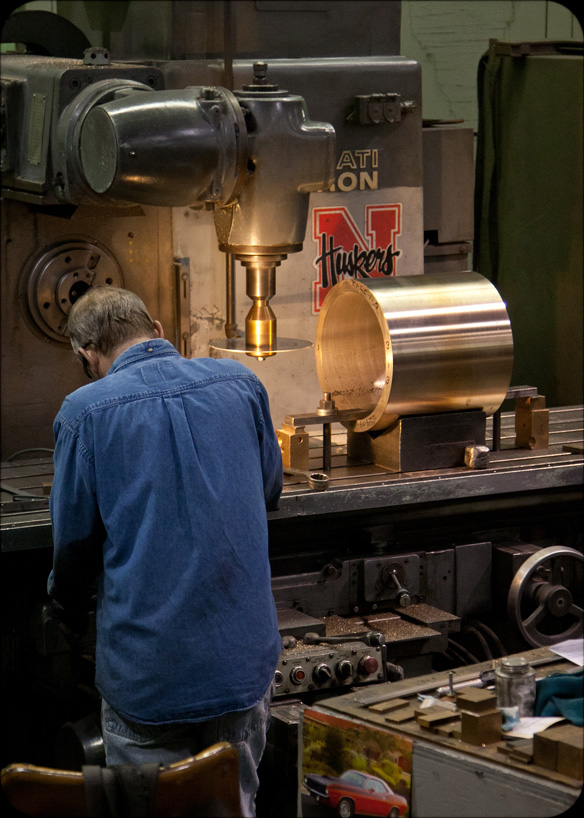
Magnolia Guarantees No Rejects
Magnolia Bronzes are guaranteed to be free from all defects. In Magnolia Bronze there are no blow-holes, no sand spots, no segregated elements, no flaws… no under-surface faults of any kind to cause rejection.
In accordance with industry practice, guarantee is limited to free placement of material returned. But why just “hope” to get a good casting? Magnolia’s quality control procedure has resulted in returns of less than 1/2 of 1% of all bronze shipped over the last 10 years. This standard of excellence combined with our special alloy and our unique casting process assures you of the best possible value in bearing bronze.